GOMMA Line d.o.o - Products
Tool workshop
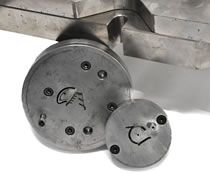
Everything starts with a great tool.Manufacturing of molds in our organization is effected by a highly skilled and experienced team consisting of rubber technologists as well as mechanical engineers. Our engineers study the needs of your products and design the mold that will provide the usability of rubber parts for your products. Our team is here to advise you on the most suitable solution for your project. We offer customizable tools for extrusion, molds for rubber injection parts and tools for specific bonding and joining of rubber products. Meeting the needs of our customers.We are specialized in custom made products based on clients specifications. Furthermore we can replicate seals and rubber parts according requirements by reverse engineering, even if the samples brought in are aged. Our reaction times enable us to guarantee short production times from the simplest to the most elaborate parts. All of our rubber products are designed according to clients needs: shape, dimensions, bonding, type of attachment, corner solutions, surface coatings. More...
EPDM rubber profiles
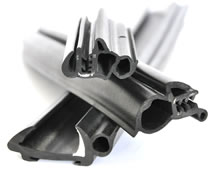
Rubber profiles that meet the industry demand and support product design.GOMMA Line’s core competence is developing sealing systems that keep the vibration and noise at a minimum level Our sealing systems are not only robust and durable in all conditions but also meet the requiered functionality terms. Our expertise offers a complete profile design. Our in-house tool workshop helps a quick product development whereas GOMMA Line’s spectrum of services assists in delivering products that fulfill products purposes. Specific, as you need it!We offer specific corner bonding solutions, at various angles and material joints. Our expertise comes great both for static and dynamic seals and is applicable for windscreens, weather strips, glass running channels and other seals. We can supply profiles in every conceivable form – with perforations or cutouts, as vulcanized molded pieces, metal inserts and diverse surfaces. More...
RUBBER MOLDED PARTS
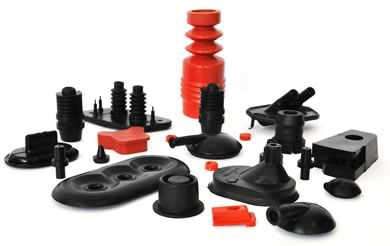
Rubber in all formsGOMMA Line manufacturing facilities include rubber injection lines as an in-house tool workshop where all projects start as a request from the customer to meet a specific need. Our team helps to develop the best possible product by advising materials, technology, and processes. We use our years of rubber expertise and tool design to produce rubber components that meet the required specification. Meeting the needs of our customers.GOMMA Line serves an array of industries as the rubber products manufacturer, including but not limited to automotive components, home appliance products, agricultural machinery, commercial vehicles and railway industry. Working together with leading raw material suppliers in Europe, we provide greater value to our partners by designing and optimizing custom molded rubber parts and manufacturing processes that address the specific needs of each program. We deliver high-precision, high-volume, and top-quality solutions to our customers. High-quality tools for superior products.Manufacturing of molds is supported by a highly skilled and experienced team of rubber technologists as well as engineers for the design and manufacturing of molds. In-house tool workshop lower product development and correction time. GOMMA Line advanced rubber molding capabilities allow us to manufacture rubber parts for your company’s needs in an infinite variety of shapes, sizes, colors, and configurations. More...
BRAKE HOSES
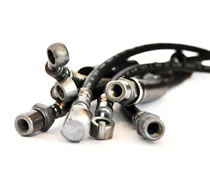
A lot more than just safety.GOMMA Line has a modern production equipment, assembly and testing of brake hoses and hoses for hydraulic clutch systems. Products produced in our plants suit demanding international standards (SAE J 1401, FM VSS 106, ISO 3996), as well as all the technical requirements and standards. Car manufacturers trust our quality.Our brake hoses are installed in the most known car models from Renault Nissan AvtoVAZ Group and UAZ. The fittings which we use have ZnNi alloy surface protection, and they are designed to meet the strictest demands of corrosion resistance (more than 1000 hours until the appearance of base material corrosion) as well as all environmental protection requirements. More...